Customer Profile
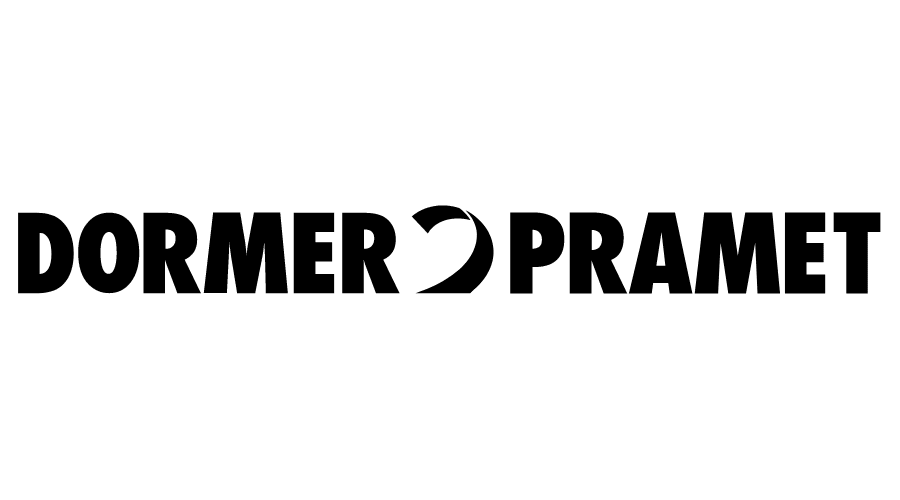
Thanks to innovative solutions and the professional approach of our partners, we are confident that our production networks are as secure as possible and ready for further expansion. Ensuring uninterrupted and safe operation is key for us.
Baseline and project objectives
The key objectives of the project were to control the access of each individual asset to the production network, including individual machines, while ensuring the robustness and security of the industrial network as a whole. The first step was to implement micro-segmentation based on the identity of each resource (one device per segment). The second step was to map the conducted communication to create communication rules. At the same time, this established the basis for the subsequent automatic detection and elimination of potential cyber threats. The customer received a unified and integrated solution based on clearly defined rules, both for access and communication. In addition, the production network as a whole was separated from the IT/administrative network by deploying a firewall with an industrial set of IDS/IPS detection signatures directly designed to protect production-specific industrial protocols.
The Cisco solution delivered is fully automated in its response to security incidents. This is not the only reason it remains easy to manage and grasp. Its integration also makes it easily portable and universally applicable, not only in other Dormer Pramet plants.
Benefits
- Increased security and protection of production machines against cyber threats
- Better control and management of access to production equipment
- Easy network management through automated responses to security incidents
- Ability to scale and expand the solution to additional sites
Popis řešení
A firewall with both detection and prevention capabilities (IDS/IPS) has been deployed at the network interface. The manifestation of a threat entering the production network will be automatically eliminated and, in specified cases, may result in the preventive disconnection of end equipment from the production network. To detect an incident within the production network, CyberVision sensors have been installed to monitor and analyse in detail the communication between production machines and their control elements. It is said that the devil is in the detail, and this is doubly true for production control. Here, it depends on each instruction to ensure that it does not deviate from the expected interval, that it comes from the expected source and that it arrives at the specified time. Anything significantly different from the expected sequence and content can be considered a potential disruption to production continuity. Of course, these values need to be monitored over the long term and only retrospectively determine the baseline.
The system was designed to provide automated responses to security incidents and simplified access management. Strict access controls have been implemented to restrict access to only authorized users or devices, both of which are possible. With micro-segmentation, a high level of isolation has been achieved - threats cannot easily spread not only between production devices, but equally between different parts of the corporate network. If a threat in the form of, for example, a contracting company's laptop being infected, it does not get out of its closed segment and thus no longer poses a risk to the rest of the production machines or even the administrative part of the network.
Key security points include:
- Identification of all industrial equipment to set appropriate security
- Isolation of inter-network zones leading to protection from threat propagation or attacker movement
- Detection of abnormal IT/OT instructions and behavior to protect production processes
- Gaining enhanced insight into event communications for further investigation
A comprehensive suite of Cisco software tools for industrial networks has been deployed, including the Firepower Management Center (FMC) firewall manager and identity and access management solutions (ISE), providing complete transparency and control over the entire production network. CyberVision sensors work together to monitor and share information inside network traffic and potential threats hidden within it. the implementation was rounded out with the deployment of Cisco Catalyst Center, for configuration orchestration and lifecycle monitoring of more than just industrial switches.
The network was designed to be easily expandable to other sites, ensuring future process security and efficiency across all Dormer Pramet production lines and related operations. This universal design ensures that safety standards are maintained regardless of geographic location or the specific requirements of individual manufacturing sites.
Used technologies
- Cisco firewalls with industrial features
- CyberVision sensors for real-time monitoring of IT/OT communications
- CyberVision center for visualization of communication flows and security events of IT/OT communication
- Cisco segmentation and microsegmentation tools
- Firewall Management Center (FMC) for security policy management
- Policy server for identity and security management (ISE)
- Cisco Catalyst switches for aggregating and managing network traffic
- Cisco Catalyst Center, for configuration orchestration and lifecycle monitoring of not only industrial switches.
DO NOT HESITATE TO
CONTACT US
Are you interested in more information or an offer for your specific situation?